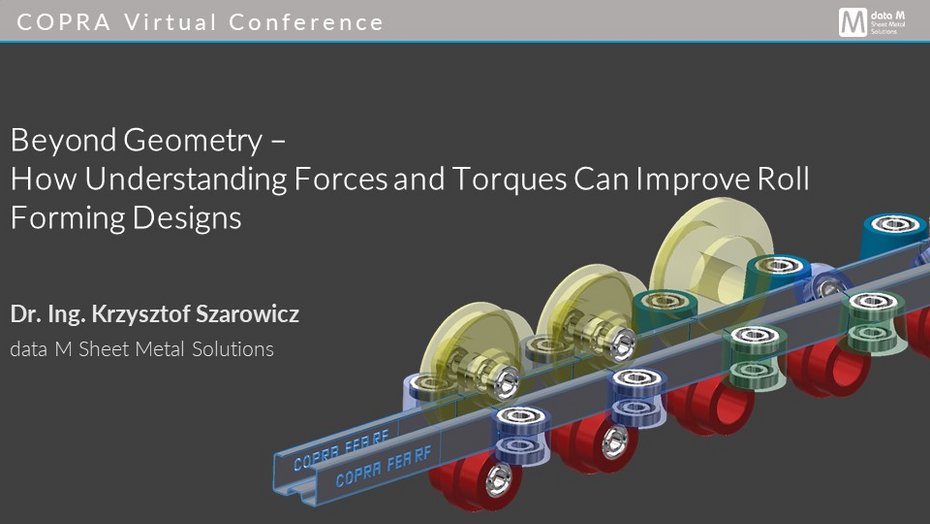
There is no sheet metal forming without the critical forces generated by the forming tools. A deep understanding of these forces—and how they interact with both the sheet and the machine components—is essential for designing high-performance roll forming systems.
Topics
During this conference, we will demonstrate how forces and related data from finite element analysis (FEA) simulations can help optimize key aspects of roll forming design, including the roll contour, bearings, machine structure, and overall product quality. Our presentation will explore:
- Leveraging COPRA FEA RF for Enhanced Design: Discover how COPRA FEA RF is revolutionizing roll forming design by accurately simulating the intricate interactions between material properties, sheet thickness, forming steps, roll gap, and friction. Learn how its sophisticated algorithms provide a detailed analysis of stress distributions and deformation patterns that are critical for optimizing roll profiles and machine configurations.
- In-Depth Force Analysis: Understand how COPRA FEA RF quantifies the forming forces that impact the sheet and the machine components. The software not only predicts marks or scratches on the sheet surface but also evaluates potential issues such as shaft deflection, bearing loads, and tool wear. This insight is invaluable for preemptively addressing issues that could lead to machine failure.
- Torque and Power Optimization: The simulation offers a comprehensive view of how forming forces translate into roll torques and, consequently, determine the necessary power to drive material through the system. We’ll explain how COPRA FEA RF assists in refining drive system design, optimizing motor control to maximize energy efficiency and reduce operational costs.
- Simulation-Driven Process Improvements: By integrating advanced FEA simulation data, COPRA FEA RF enables engineers to simulate real-world operating conditions, including dynamic loads. This capability helps in validating design choices, predicting machine behavior under stress, and planning maintenance schedules to enhance reliability.
Join us for a 30-minute session at the COPRA Virtual Conference where Krzysztof will share practical examples and case studies demonstrating how using COPRA FEA RF can lead to significant improvements in roll forming designs, machine reliability, and overall product quality. This session is an excellent opportunity for engineers and designers to learn how simulation-driven insights can be a game changer in the roll forming industry.
Presenter
- Dr. Ing. Krzysztof Szarowicz studied at the Silesian University of Technology in Gliwice (Poland). With his thesis “Analysis of Deformations of Cold Rolled Profiles Used in Cars” he obtained his post graduate degree in sheet metal forming in 2008. Krzysztof worked at the university as research engineer before joining data M Sheet Metal Solutions GmbH in 2009. As Design Engineer, he is working on complex design projects for open, closed and welded sections. Krzysztof loves travelling around the globe giving customer support and trainings for international clients – and of course offers these services also online.
Date
- 2025-04-29 2.00 pm CEST
Location
- Online-Presentation
Language
- English